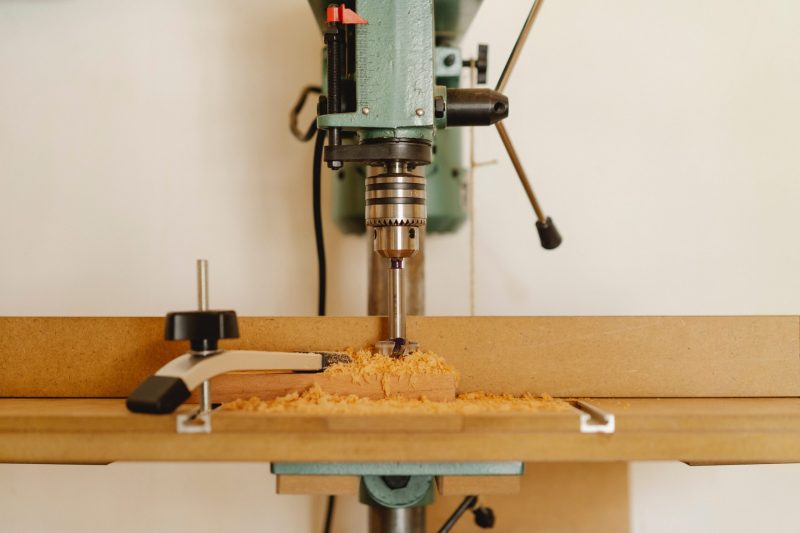
Thousands of manufacturing industries rely heavily on CNC lasers or mechanical cutting machinery for fabrication needs. Both methods are used widely and perform the same essential metal cutting tasks. However, they differ in many ways, and most industries opt for one over the other. Each is identified by its own equipment and comes with specific benefits and disadvantages.
Deciding which machine to use for your manufacturing needs will depend on several factors. Some of the most common variables between the two techniques include differences in production capabilities, cost efficiency, and equipment requirements.
If you want to know more about your metal cutting options, Steelway Laser Cutting can provide you with all the information you need to make an informed decision that will save you time and money. We have extensive experience in metal manufacturing. Our team of experts can help you decide if an industrial CNC laser cutter or mechanical cutting machine is right for your fabrication needs.
What is Mechanical Cutting?
This cutting technique utilizes power-driven equipment, including tooling and machining, to cut any material into shapes according to the intended design specifications. Mechanical cutting uses different machines, such as drill presses, lathes, and milling machines, each with its purpose.
Machines Used in Mechanical Cutting
Lathe
- This metalworking machine spins materials while a cutting blade removes excess stock to create the desired shape. Cutting fluid is used to maintain temperature control, lubricate moving parts, and remove debris from the workpiece.
Milling Machine
- A milling machine secures the workpiece to a stationary cutting tool and a movable table. Manual or computerized directions move the table around the rotating blade to make the desired cuts, making milling machines capable of creating complex and symmetrical shapes across axes.
Drill Press
- This is a stationary drill mounted to a table or bolted to the floor and driven by an induction motor. It consists of a base, a pillar, a table, a spindle, and a drill head. Cylindrical holes in the workpiece are produced by a three-pronged handle that raises and lowers the drill bit. Also, as the drill bit spins and cuts the metal, it carries debris out of the hole.
Advantages of Mechanical Cutting
- Mechanical cutting can perform many cutting operations on one machine, such as steps, perfect angles, drilled and tapped holes, beveling, and radii.
- With proper techniques and tools, mechanical cutting can also hold incredibly tight tolerances within 1/10 of 1/1000th of an inch.
For example, lathes are ideal for complex shapes like round hubs, shafts, rollers, and cylindrical objects. On the other hand, mills cut square and complex-shaped objects with three-dimensional stepping and holes.
Mechanical cutting is significantly cheaper than laser cutting, making it easier to integrate into manufacturing services. However, this is the primary reason for its continued use in most current industries.
Disadvantages of Mechanical Cutting
Material contamination can be an issue when using mechanical cutters. This often requires post-machining treatments, additional steps, and precautions. This makes mechanical cutting less streamlined and less efficient than laser cutting.
What is Laser Cutting?
This innovative, more efficient cutting approach utilizes a high-powered light beam to cut virtually any material. A CNC (computer numerical controlled) laser machine is extremely accurate and significantly decreases the likelihood of an error.
Advantages of Laser Cutting
- There is no direct contact between the laser device and the cut material. Lasers create fewer and smaller heat-affected zones. The elimination of contact reduces the possibility of contamination or damage to the equipment and the material itself, preventing wear and tear or deformation. This is vital when it comes to parts being manufactured for certain industrial applications. The food industry is one example of where contamination prevention is critical.
- Laser cutting edges and finishes material while it cuts the parts from the sheet of steel, resulting in smooth polished, high-quality cuts. With no other work needed, manufacturing can be as simple as cutting and delivery or assembly. This advantage makes metal manufacturing and fabrication more organized and streamlined than mechanical cutting.
Common Uses for Laser Cutting
Laser cutting is beneficial for the mass production of parts that can be cut from sheets of material and work as effectively as sheet metal bending tools. Parts ideally manufactured with laser cutters include washers, plating with complex holes and slots, latches, and more that can be cut out on a laser table in large quantities relatively quickly.
- Metal bending and welding
- Cutting
- Engraving
- Marking
- Etching
- Perforating
- Seaming
- Drilling
Industries That Benefit from Laser Cutting
Industrial CNC laser cutters can optimize processes, applications, and production across various industries. Laser cutting is an efficient way of generating high-volume products in a short time frame. The ability to produce accurate, clean, and precise lines and cuts and detailed finishing makes laser cutting ideal for a wide range of industries that manufacture the following products.
- Medical equipment
- Electrical
- Automotive manufacturing
- Musical instruments
- Agricultural
- Contract manufacturing
- Military
- Construction
Advantages of Investing in Laser Cutting
- Savings in tool costs
- Increase in material yields
- Implements design flexibility
- Precision level and edge quality
- Controls the depth of cuts
- Ensures worker safety
Steelway Laser Cutting Professionals Are Your Trusted Experts in Metal Cutting
Weighing the benefits of one type of cutting versus the other essentially comes down to pros and cons. A mechanical cutting machine is easy to use and cost-efficient but risks of damaging or deforming the material being cut. For an industrial CNC laser cutter, balancing its precision and reliability against its cost and energy usage is the dilemma. Without the constraints of cost-efficiency, laser cutting is the optimal choice.
If you’d like to learn more about how laser cutting can enhance your company’s metal fabrication process, contact the team at Steelway Laser Cutting. We are professional metal cutters with years of experience and exceptional customer service. Let us show you how we can handle your metal manufacturing needs from design to delivery.
Contact us today.
Article reviewed and approved by Director of Product Design – Derek McAvoy.